Of course we could but if any of you are like me, you have bits and pieces of material that will not go away. This is something I have seen elsewhere before but the idea was a spontaneous one, based on that swivel pin that has been floating around in my tool box for I know 3 years. Watch, I will need it tomorrow as the answer to some fabrication prayer.
I have the axle welded, and then a piece of pipe shoved down on that for a wear surface instead of it spinning on the weld and different spacers for different degree angles. I will weld the thrust spacer in place once I am sure it's how I want it. Also, I am going to come up with a non skid support system so it stays put. Maybe 1" pipe nipples with rubber crutch feet on them. Typically, I just cobble things together as I go but I stopped myself this time. I have time to "think" about it. I am also going to make a little drawer that fits into the channel to store the different degree spacers, and some nylon friction washers perhaps and a bottle of oil. A clip system to attach different grits of wet/dry paper on the sliding T-bar.
Figure a stop for the blades as well but I am not decided on how exactly I want to approach that just yet. Something adjustable would be nice.
Any/all ideas welcome.
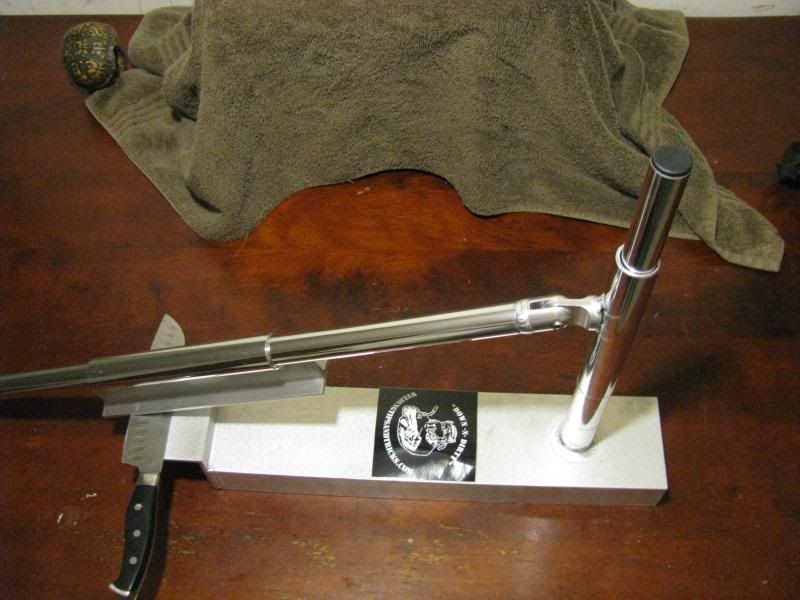
I even went as far as to chamfer the pipe ends and polished them on the rouge wheel. Some lemon pledge on the moving parts and she is slick as a whistle.
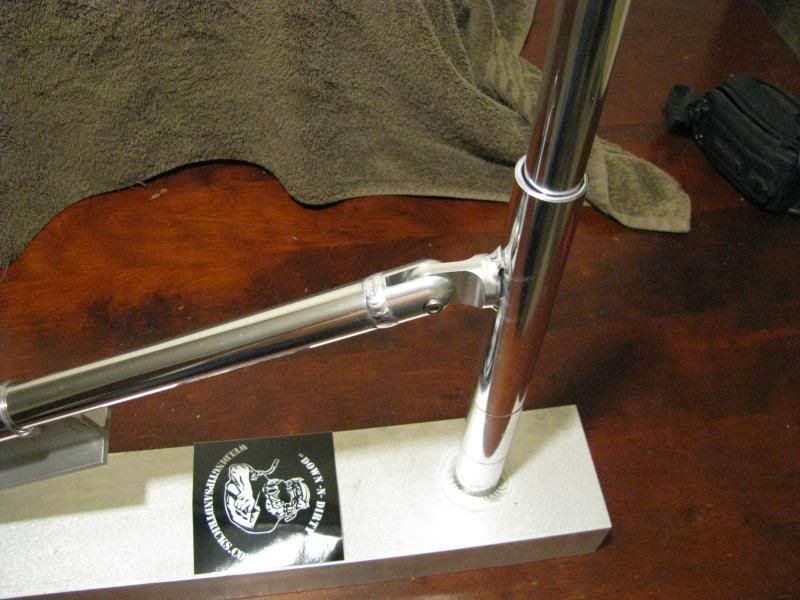
Just got the T-shirt from WT&T and this decal came with it. I didn't stick it but figured it might stand in for a photo op.

Here's the collection of parts. Minimal welding to save from distorting the larger tube that needs to slide freely without any gall spots and I really don't feel like polishing the inside.
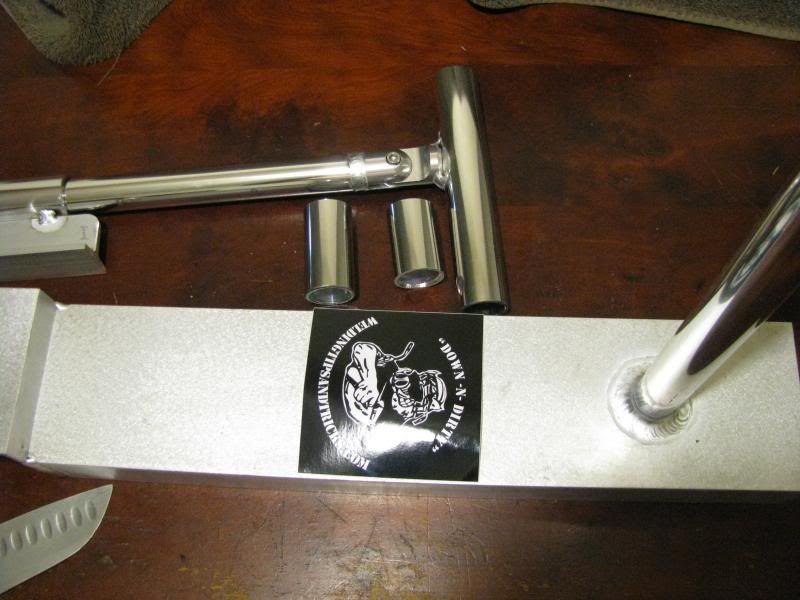
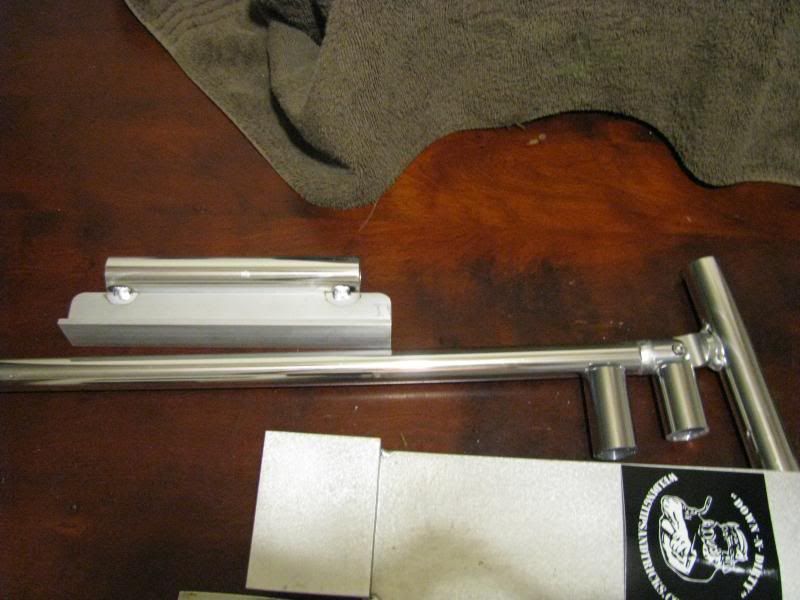